Finance & Business
What Startups Can Learn From The History Of Automation
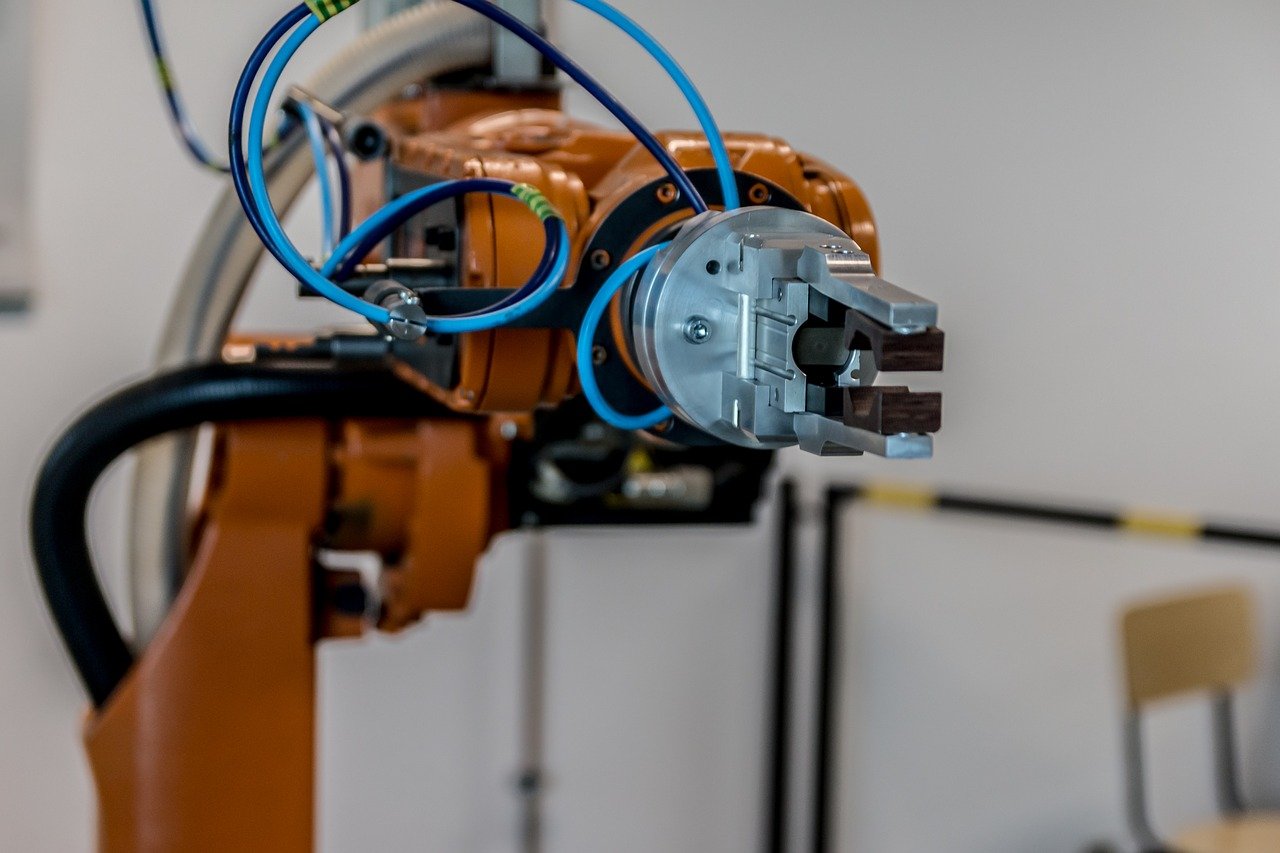
Automation is not new. In fact, it has been with us since the invention of the mechanical loom. IT expert Robert Weiss explains why looking back helps us to take advantage of automation’s opportunities in the future.
Marketers are true geniuses when it comes to selling old wine in new skins. A memorable example is virtualization – IBM demonstrated this as early as 1970 with the VM/370 operating system in the System/370. Or cloud computing – as early as 1995, the Fraunhofer Institute demonstrated the BSCW groupware, by definition a cloud approach. And digitalization, which is on everyone’s lips, is simply the same as the old automation.
Digitization: curse or blessing?
If you look for the origins of digitization in components or systems, you have to refer to Konrad Zuse’s Z3 from 1941, the world’s first functioning computer based on floating point numbers and binary circuit technology. Other historians, especially from the USA, see the first microprocessor from 1971 as the beginning of digitization. With the 4004, Intel introduced the first freely programmable integrated circuit, a component that was to significantly change our lives.
The fear of this component was very great in the media. The job killer was launched. Robots are conquering our jobs! Unemployment was to rise sharply. The federal government reacted with two impulse programs by Waldemar Jucker at the end of the 70s and the beginning of the 80s. The result from today’s perspective: the microprocessor ultimately led to significantly more jobs.
And today we are presented with exactly the same picture, the microprocessor has been replaced by Industry 4.0, the smart factory. Again, politics is needed to free our manufacturing industry from its immense cost pressure and to prevent or limit the outsourcing of production abroad. But it is precisely modern automation that could play an important role in preventing this in high-wage countries like Switzerland. Only the opportunity must not be missed.
Industrial revolutions as a time mirror of industrial epochs
The development of automation can be divided into four different phases, which are often referred to as industrial revolutions.
The first industrial revolution was based on the introduction of mechanical production systems using water and steam power. The starting point for this was the mechanical loom at the end of the 18th century.
At the end of the 19th century, the introduction of mass production based on the division of labor with the help of electrical energy began, and with it the second industrial revolution. The first assembly line was introduced in the slaughterhouses of Cincinnatti in 1870.
The use of electronics and IT to further automate production started the third industrial revolution at the beginning of the 1970s. The first product here was the Programmable Logic Controller (PLC), the Modicon 084, in 1969.
And today, as part of the fourth phase of automation, we celebrate Industry 4.0, which is based on cyber-physical systems and allows us to realize intelligent factories or smart factories.
What are the distinguishing features of the 4th industrial revolution?
In general, cyber-physical systems comprise a high level of complexity. They are designed to be very IT-heavy and their control is on the one hand via the market, but also via the infrastructure (embedded logic) itself. Traditional manufacturing is being replaced by additive manufacturing, enabling rapid prototyping and rapid manufacturing. This will result in a shift from mass production to make-to-order production, which offers entirely new opportunities.
With individual production, the previous production cycle is also closed: from artisanal production in the mid-19th century to mass production from the mid-1950s to individualized mass production from the 1980s via lean manufacturing to personalized production with reconfigurable manufacturing systems (smart manufacturing).
What is also new is the view that a factory must present itself in a global environment with a wide variety of influencing factors such as energy, product, mobility, logistics and infrastructure. This forces companies to rethink, taking into account people, organization, dynamics, individuality, volatility and connectivity.
But is there a willingness to do this everywhere? That is the big question.